What?
-
Designed and fabricated electronics to position and control the shape of ultra-thin deformable mirrors for space applications
-
Optimized PCB layout to protect MCU from browning out due to close proximity to fast switching high-voltage line
-
Tested and validated boards for space applications

How?
-
Improved PCB layout from EE engineer using Autodesk Eagle
-
Measured EM field to understand correlation between MCU shutdown and fast switching of HV lines for picomotor control
-
Experimented with different shielding options from external copper shields to PCB ground plane layers (final solution)

Results
-
Boards built and assembled inside mirror payload assembly
-
Boards tested in a thermal vacuum chamber replicating the thermal cycles expected by the satellite AAReST during its mission in low earth orbit
-
Boards certified for space application (TRL 8) after successful thermal, vacuum, vibration, and shock tests
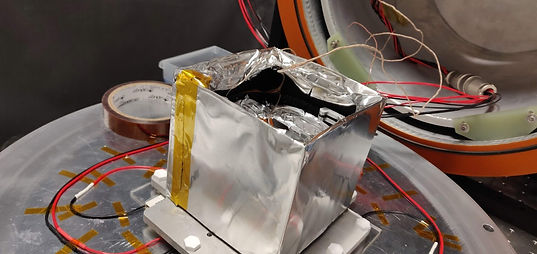